In recent years, power supply analysis has become increasingly complicated. The variety and number of components have increased rapidly. The use environment has also become harsh and diversified. The electronic systems being served are becoming more and more important and expensive, especially for military equipment, especially for aviation. The requirements for components and system reliability in aerospace are even higher.
The task of the power supply in the electrical system is to provide electrical energy for various circuits in the electrical system. Because the types of circuits have different functions, the power supply can be divided into different types based on the supply methods: UPS power supply, EPS power supply, and power supply , Frequency conversion power supply, purification power supply, special power supply, generator set, switching power supply (AC/DC), inverter power supply (DC/AC), module power supply (DC/DC) and other power supplies.
What are the thermal imager applications in the power supply?
The temperature control of the power supply is an important way to improve the reliability and service life of the power supply module and system. In the design and application of power supply, choosing the right components, that is to reduce the circuit loss, improve the module conversion efficiency, and select a reasonable cooling method is the key technology to ensure the reliable and stable operation of the power supply. Combining the two organically, it will make the power supply have It has the advantages of stronger environmental adaptability, long life, low cost, and easy maintenance.
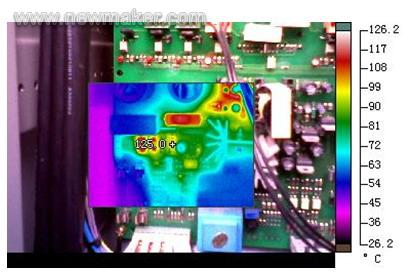
The thermal imager can provide a heat map of the thermal conditions at work for each component in the engineer's circuit. It helps engineers analyze the effects of components on the temperature of the entire power supply circuit, and can also help engineers select the appropriate load capacity conversion module.
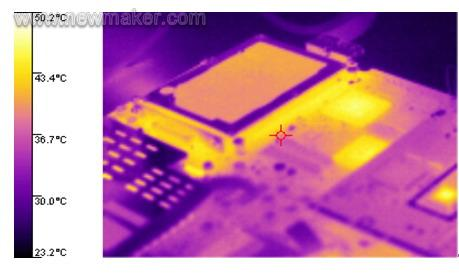
The thermal imager can provide accurate transformer temperature through quick and easy operation.
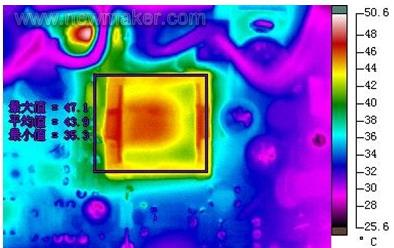
The thermal imager can help engineers analyze the temperature distribution of the entire circuit board through the provided infrared heat map, and improve the design and application of engineers.
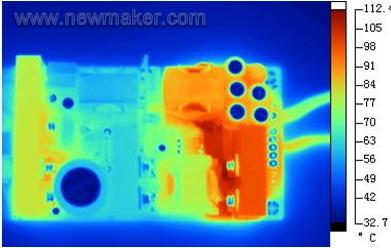
4) Power supply cooling Power supply cooling technology is a basic means to meet various technical performance requirements of the industry. At present, the common cooling methods for each power module include natural cooling, pure fan cooling, natural cooling, and fan cooling.
There is a large transformer in the power supply product, and some large capacitors. These are large heat sources. These heat sources may affect the stability and service life of some other circuits and their components inside your product. . With the use of an infrared thermal imager, it is possible to measure the heat generation and heat dissipation in three situations very directly. Engineers improve the design, use reasonable cooling measures in practical applications, improve the reliability of the power supply, and reduce the failure rate of the equipment.
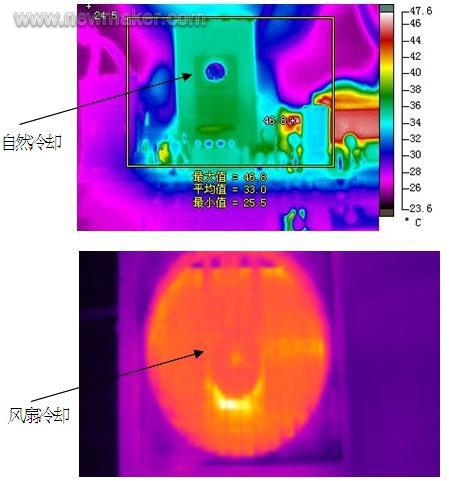
Thermal imager in the power company's application department, in addition to R & D department, also mainly include: quality control department, after-sales service department and equipment maintenance and other departments.
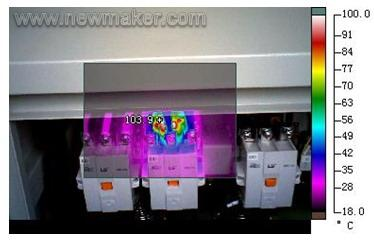
Unique Applications of Infrared Thermal Imagers 1. Existing Temperature Analysis Tools For the R&D and application of power supplies, due to their specificity, many engineers complain that existing tools cannot support them in performing a detailed and comprehensive temperature field depiction. Inconvenient operation, and may change the original temperature field distribution, such as: In the current power supply development and application, the temperature analysis tool is a data collector, but the use of data collector may encounter the following problems: circuit board power off, patch There are not enough thermocouples, the operation is inconvenient, the reaction time is slow (30 seconds to 1 minute), and the use of a data collector will also change the thermal conditions of the devices under test. At the same time, the temperature field distribution and thermal analysis of the entire power supply cannot be analyzed.
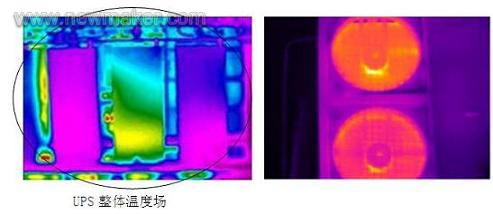
2. Thermal Imager Temperature Analysis Advantages Compared to infrared imager, data collector and infrared point thermometer, infrared imager has its own advantages:
a) When the target circuit is detected by an infrared thermal imager, there is no need to power off, and the operation is convenient. At the same time, the non-contact measurement makes the original temperature field undisturbed.
b) The reaction speed is faster, less than 1 millisecond;
c) With the help of the supporting infrared analysis software, the user can perform detailed and comprehensive analysis of the obtained power supply temperature data at the site without generating a complete temperature report.
This article summarizes the thermal imager in the power industry can play its superiority, because it has unique advantages, can supplement the lack of traditional detection methods. However, there is still a lot of work that needs further improvement and improvement in the future practice, making the application of infrared thermal imaging technology in the power supply industry more extensive and scientific, effectively improving the quality of power supply products, improving the power conversion efficiency, and improving the system performance level.
Zinc is one of the most versatile die cast metals. It provides higher precision with lower tooling costs when compared to other die cast metals like aluminum or magnesium. Zinc Die Casting also offers a broad range of excellent physical and mechanical properties, finishing characteristics, and is the easiest to cast. Die casting is a versatile, efficient and economical process for producing engineered metal parts.
Die casting offers a broader range of shapes and components than any other manufacturing technique. The die casting process requires a steel mold. These reusable steel molds, called dies, can be designed to produce complex shapes with a high degree of accuracy and repeatability. The dies are mounted into a machine that injects molten metal into the dies under high pressure. Once the molten metal has solidified, the die is opened and the casting is ejected from the mold. The die is then closed and the process starts over.
Zinc Die Casting,Casting Zinc Alloy,Die Casting Zinc,Die-Cast Zinc Alloy,Zinc Alloy Die Casting
NINGBO CITY YINZHOU RUICAN MACHINERY CO.,LTD , https://www.ruican-casting.com