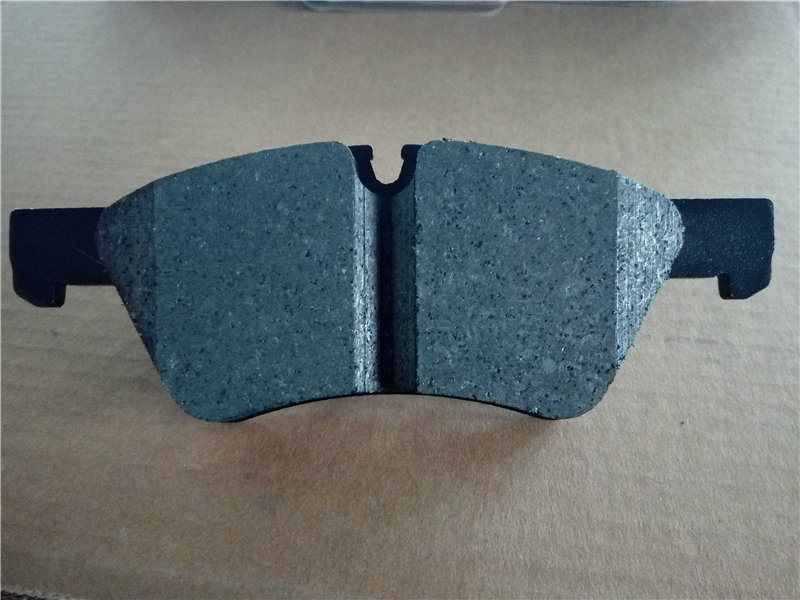
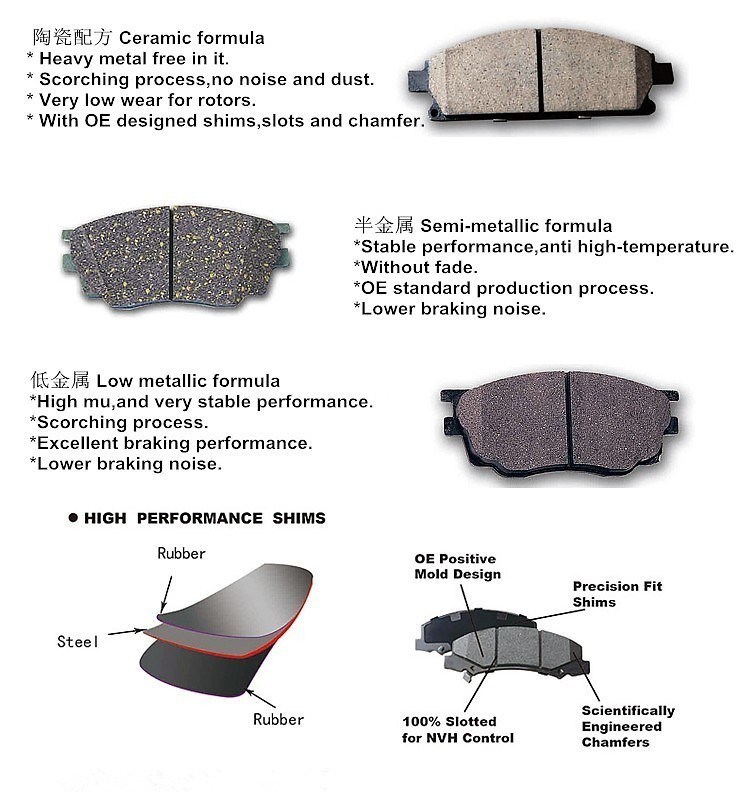
Â
WHY US
strictly selected and tested raw material for each product
precise proportioned formulation proven with consistent braking performance
detecting equipment promising quality under control
customized packaging/ adapted manufacturing.
product descriptions
reference | brake pad |
material | low-metallic/semi-metallic/ceramic |
certificate | TS16949/ISO9001 |
packing | boxes/cartons/pallets |
braking performance | ultra quiet/low dust/no asbestos |
MOQ | 50 sets per item |
port of shipment | Qingdao port |
delivery time | 25-25 days |
 Welcome to our factory.
Test Bench
strict quality control system
WorkshopÂ
Packaging
Â
Company profile
Baotai adopts domestic and foreign leading production equipment and advanced technology formulas. We manufacture brake pads, brake discs, brake block, wheels, tyres, etc.
Our precision-machined DNET brake pads are suitable for the domestic and international market demands. The perfect technology, advanced equipment and strict quality control system ensure the quality of DNET brake pads the leading position in domestic and abroad.
DNET brake pad can cover more than 95% of the vehicle models in the global market, which can meet the demand of braking under various driving conditions.
Â
Frequently Asked Questions
How do IÂ track my order?
After placing your order, an email is sent to you containing a copy of your order and order number. When your order deliver, you will also receive an email from Brake Performance with your tracking numbers. You can check your delivery schedule on our website under "Order Tracking" and enter your order number, name, or email address to track your order. Alternatively, you can go to ups.com and track it from there.
How does your lifetime warranty work?
If you have an issue with any of our Lifetime Warranty products, simply deliver the product back to us and we will deliver you out a new replacement, without harassment. Refer to our product warranties at the bottom of the page, under warranties and policies.
Thermoforming is a manufacturing process used to shape plastic sheets into various custom design products. It involves heating a plastic sheet until it becomes pliable, then using a mold or a vacuum to form it into the desired custom shape.
Thermoforming and vacuum forming are both processes used to shape plastic sheets into specific forms. However, there are some differences between the two techniques:
1. Process: In thermoforming, a plastic sheet is heated until it becomes pliable, and then it is pressed against a mold using pressure or a vacuum. Vacuum forming, on the other hand, relies solely on the use of a vacuum to draw the heated plastic sheet onto the mold.
2. Mold complexity: Thermoforming is typically used for more complex shapes and intricate molds, as it allows for greater detail and precision. Vacuum forming, on the other hand, is better suited for simpler shapes and molds that do not require as much detail.
3. Material thickness: Thermoforming is often used for thicker plastic sheets, typically ranging from 0.030 to 0.250 inches in thickness. Vacuum forming is more commonly used for thinner plastic sheets, typically ranging from 0.005 to 0.060 inches in thickness.
4. Production volume: Thermoforming is generally more suitable for high-volume production due to its faster cycle times and ability to handle larger sheets of plastic. Vacuum forming is better suited for low to medium volume production, as it has slower cycle times and is limited by the size of the vacuum forming machine.
5. Cost: Thermoforming typically requires more expensive equipment and molds, making it a more costly process compared to vacuum forming. Vacuum forming, on the other hand, is a more cost-effective option for smaller production runs or prototypes.
Overall, thermoforming is a more advanced and versatile process that offers greater precision and complexity, while vacuum forming is a simpler and more cost-effective option for less complex shapes and smaller production volumes.
Thermoforming is a versatile process that is widely used in industries such as packaging, automotive, aerospace, and medical. It offers advantages such as cost-effectiveness, quick turnaround times, and the ability to produce complex shapes with high precision.
Custom Thermoforming,Thermoforming Plastic Products,Thermoforming Process,ABS Thermoforming
Dongguan Yiyongli Industrial Co.,Ltd. , https://www.dgthermoforming.com