3. The top of the diesel Engine Piston often has a variety of pits, and its specific shape, position and size must be adapted to the formation and combustion requirements of the diesel engine mixture.
The production process of a piston usually involves several steps, including casting, machining, heat treatment, surface treatment and assembly.
1. Casting: The first step in the piston production process is casting. This involves pouring molten metal, such as aluminum alloy or cast iron, into a mold to form the desired piston shape.
2. Machining: Once the piston is cast, it is machined to perfect its shape and size. This involves using cutting tools, such as lathes and milling machines, to remove excess material and create the final shape of the piston.
3. Heat treatment: After processing, the piston is usually heat treated to improve its mechanical properties. This involves subjecting the piston to high temperatures and then cooling it slowly to achieve the desired level of hardness and strength.
4. Surface treatment: The piston is then subjected to surface treatment, such as anodizing or coating, to prevent wear and corrosion. Anodizing involves forming a protective oxide layer on the surface of the piston, while coating involves coating a material, such as ceramic or polymer, on the surface of the piston.
5. Assembly: Finally, the piston is assembled into a complete engine assembly with other components, such as piston rings and connecting rods.
The installation process must properly assemble the piston and other components together to ensure the normal operation and performance of the engine.
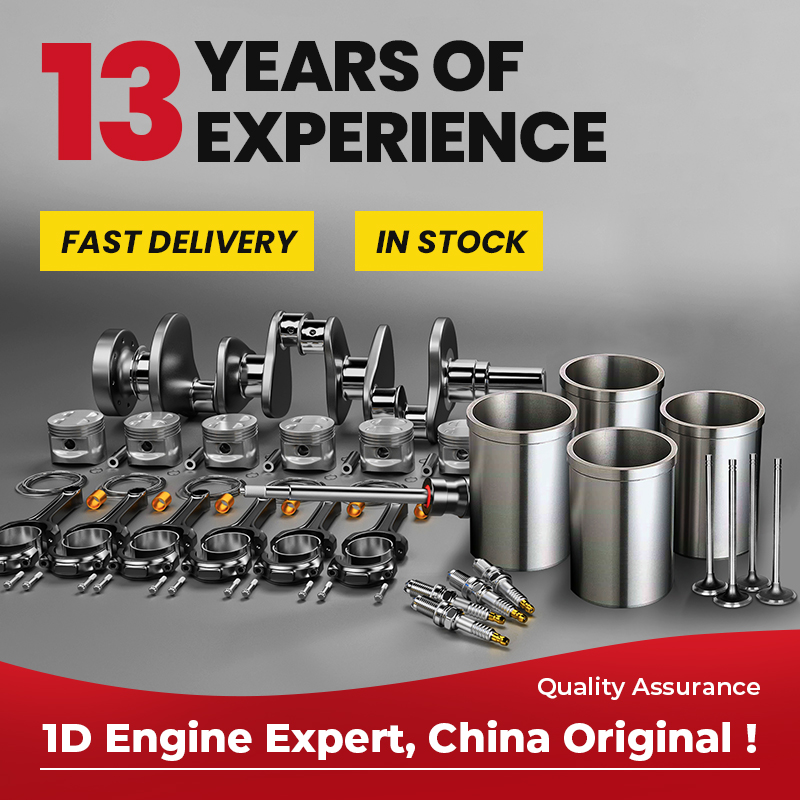
MITSUBISHI Piston set,Engine piston set for MITSUBISHI,Original piston Set,Original MITSUBISHI Engine piston
1D auto parts , https://www.1dauto.com