Introduction: The spraying machine is mainly used to convey concrete to the nozzle of a manipulator through concrete pipes through a pipeline, and uses compressed air with an accelerating agent to spray the concrete onto the walls of the roadway to be sprayed. This is a new type of high-efficiency spraying machine, and the concrete is sprayed. As the most commonly used shotcrete support equipment, the machine plays a very important role in the construction. Shotcreting machines are widely used in tunnels, culverts, engineering buildings, mines, subways, hydropower projects, underground engineering and shotcrete construction of roadways in coal high marsh mines; various types of industrial furnaces, refractory lining refractories or forming repair; In the construction of slope protection and greening, the soil is transported and injected.
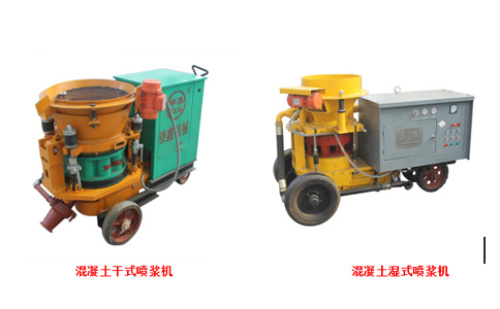
What is the difference between dry spray guns and wet spray guns in concrete spraying machines? Below we mainly introduce the following aspects:
1. Spraying mode is different between dry spraying machine and wet spraying machine.
Dry spray guns are filled with dry cement or concrete aggregates in the hopper. When spraying, water needs to be added at the joints of the machine nozzles to ensure the spraying effect of the spray gun, but more dust will be produced. The physical harm to workers is greater.
Wet spraying machine is the cement or concrete aggregates and other water evenly stirred to form a wet material and then spray, the machine nozzle does not need to add water, no dust, less harm to the workers body, to ensure the working environment And save material.
2. The difference between safety and operator in dry spray gun and wet spray gun
Dry shotcreting machines generate large amounts of dust during shotcreting. They have relatively large environmental pollution and physical damage to construction workers. This is not conducive to underground construction and operation of machines. Dry sprayers require more operators.
The slurry of the wet spraying machine is mixed well in advance, does not take up a lot of manpower, does not generate dust, is less harmful to the environment and workers, and can be used in various working environments.
3, dry mortar and wet mortar resilience and cohesion are different
The resilience rate of the dry spraying machine is also large, and it may cause the poor cohesiveness. In particular, downhole construction may be deformed due to changes in the earth's crust, which may easily cause splitting and destruction.
The wet rate of the wet spraying machine is relatively small. The slurry of the spraying machine is mixed well with the water-cement ratio in advance, the cohesion of the slurry is relatively high, and the deformation and deformation of the crust is small.
4ã€Dry spraying machine and wet spraying machine have different conveying distance and wind pressure
The maximum conveying distance of dry spraying machine can exceed 200 meters.
The slurry sprayed by the wet spraying machine is a well-mixed wet slurry, which is slightly weaker in the conveying distance.
Oxide powder for thermal spray refers to a type of powder material that is used in thermal spray processes. Thermal spray is a coating technique where a material in powder form is heated and propelled onto a substrate, forming a coating.
Oxide powders are commonly used in thermal spray applications due to their high melting points, excellent wear resistance, and thermal insulation properties. They can be used to create protective coatings on various surfaces, such as metals, ceramics, and plastics.
Some common types of oxide powders used in thermal spray include:
1. Aluminum oxide (Al2O3): This oxide powder is widely used for its high hardness, wear resistance, and thermal insulation properties. It is commonly used for coating applications in industries such as aerospace, automotive, and electronics.
2. Zirconium oxide (ZrO2): Zirconium oxide powder is known for its high melting point and excellent thermal barrier properties. It is often used in thermal spray coatings for gas turbine engine components, where thermal insulation is critical.
3. Chromium oxide (Cr2O3): Chromium oxide powder is used for its high hardness, corrosion resistance, and wear resistance. It is commonly used in applications where high temperature and abrasive wear resistance are required.
4. Titanium oxide (TiO2): Titanium oxide powder is known for its high refractive index and excellent UV resistance. It is often used in thermal spray coatings for optical and decorative applications.
These oxide powders can be applied using various thermal spray techniques, such as flame spraying, plasma spraying, or high-velocity oxy-fuel (HVOF) spraying. The choice of oxide powder and thermal spray technique depends on the specific application requirements and desired coating properties.
Oxide Ceramics Powder,Pure Aluminum Oxide Powder,Chromium Oxide Ceramics Powder,Yttria Stabilized Zirconia Powder
Luoyang Golden Egret Geotools Co., Ltd , https://www.xtcmetalpowder.com