→ bigger space between tie-bars
→ central-clamping structureÂ
→ famous componentsÂ
→ energy saving with servo motorÂ
→ low noise, fast responsÂ
→ high precision, Stable and super long life
→ T-Slot PlatenÂ
→ abundant Spare Parts
→ better priceÂ
Â
Clamping Unit:
1. Optimized Platen Design with high rigidity and enlarged space between tie barsÂ
2. Euromap-based Platen Layout with both T-slot &Â tap holes, locating design in moving platen to better suit various moldsÂ
3. New ejection system design with longer ejection stroke, bigger space and better rigidityÂ
4. Hydraulic drivien gear-type mold height adjustion mechanismÂ
5. Relocation of mechanical safety interlock for easier operationÂ
6. linkage structure for front connecting rod increases connectingrod's strength greatly, as well as the whole clamping unit's rigidity &Â accuracy.
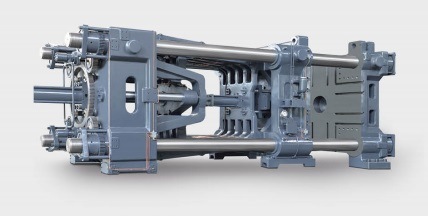
Â
Injection Unit:
1. High Quality Linear Motion Guide ensure the smooth &Â accuracy of injection processÂ
2. High Speed &Â Pressure injection structure can improve the injection speedÂ
3. Twin nozzle cylinder ensures more even &Â stable structureÂ
4. Specilized screw barrel design for various appliance
Â
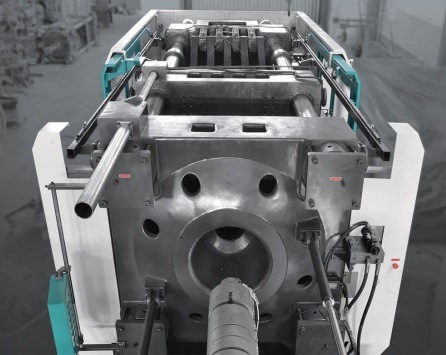
Hydraulic System:
1. The double proportional compound valve control system pressure &Â flow, highly sensitive &Â stableÂ
2. Imported high quality Pump, low in noise, long in lifespan &Â stable in performanceÂ
3. World-famous servo hydraulic system optional, better performance in lower noise &Â energy savingÂ
4. The precise feedback control of servo system to the pressure &Â flow, with higher sensitivity &Â more accurate repeatability precisionÂ
5. High performance hydraulic valve, less failure, fast switch, convenient maintenanceÂ
6. Low pressure mold protect system, which is more suitable for the precise mouldÂ
7. Greese &Â lubrication oil in dependent lubrication system can lubricate everywhere in the best situation
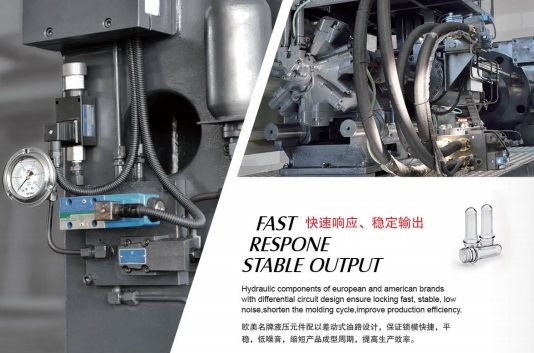
Â
Electrical System:
1. Control by double CPU, the system HMI use X86 300MHz technical grade display. The system employees a RISC 140MHz microprofessor, with high speed, noise-immunity, fan-less and lower power consumption, independent control structure improve the stablity of controlÂ
2. 8.4" display screen with resolution 800*600, user friendly screen &Â optional choose of languageÂ
3. Equiped with USB(2.0) port &Â ethernet(100-base T) portsÂ
4. 32 Points input &Â output, entendable and trouble spot can be replaced easilyÂ
5. Linder transducer's resolution is 1/65535, more precise in controlÂ
6. 120 technological parameters access can be stored &Â uploaded with an ordinary USB drivesÂ
7. Injection End and temperature tracking is curve display, dynamic recorder parameter is modified, dynamic warningis exhibited, all these make the operation more convenient.
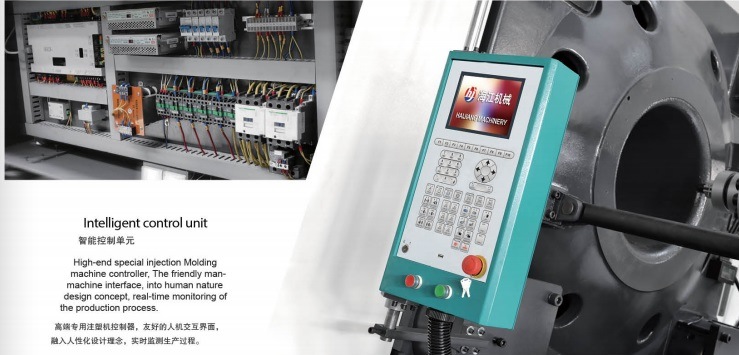
Â
Servo Controller Part:
1. High Precise Control The servo system can control the machine's pressure, speed & location precisely, make sure that the error of  accurate repeatability precision for the shot measurement is <0.3%Â
2. High sensitive response Because the motor vector is matched with the controller accurately, it only takes 0.5sec. inputing the number from 0Â to max. Compared with other traditional hydraulic injection molding machine, HJ series is more faster in speed with shorter cycle time and high efficient in productionÂ
3. Low noise Compared with traditional fixed pump &Â variable pump system, the noise is 1/10 lower under normal circumstance, more suitable for sealed dustless workshopÂ
4. Energy Saving Overall efficiency is 10% more &Â driving capacity is 18% more than common machine. This series can save 40-80% energy, and achieve first-class energy efficencyÂ
5. Water cooling saving The system condition prevent high pressure uploading without any power output, leads to the water cooling saving
Â
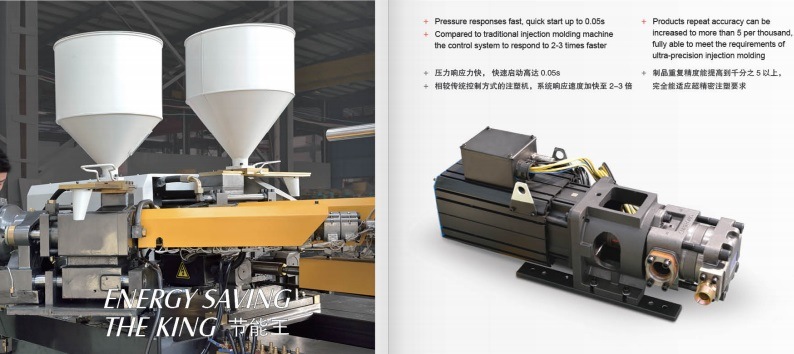
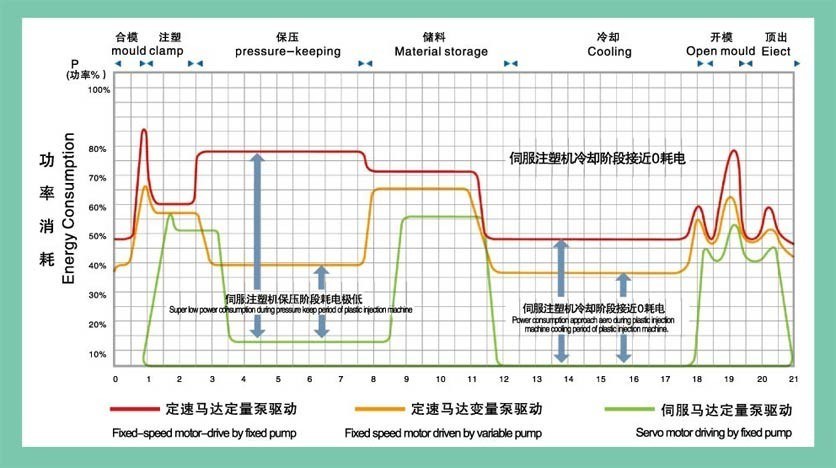
Parameter | Unit | HJF118-F5 | ||
Screw diameter | mm | A | B | C |
35 | 38 | 40 | ||
Screw I/D ratio | L/D | 23.9 | 22 | 20.9 |
shot volumn (theoretical) | Cm3 | 154 | 181 | 201 |
injection weight(PS) | g | 141 | 165 | 183 |
injection rate | g/s | 80 | 95 | 105 |
injection pressure | Mpa | 219 | 186 | 167 |
screw speed | r/min | 0~220 | ||
clamp force | KN | 1180 | ||
opening stroke | mm | 340 | ||
space between tie bars (W*H) | mm | 370*370 | ||
max mould height | mm | 400 | ||
min mould height | mm | 150 | ||
ejector stroke | mm | 100 | ||
ejector force | KN | 33 | ||
ejector number | PC | 5 | ||
max pump pressure | Mpa | 16 | ||
pump motor power | KW | 11 | ||
heating power | KW | 6.5 | ||
machine dimension | M | 4.2*1.25*1.8 | ||
machine weight | T | 3.5 | ||
oil tank capacity | L | 210 |
Â
FAQ
Q1. What is the warranty for the injection molding machine
A1:Total 18 month,Included machine platen,base,injection unit,clamping unit.
Q2:Can you sending engineer to oversea install machine and trainning customer's workers.
A1: Yes,We will send engineer to customer factory install the machine or trainning customer's workers. in one week,total free.
        After one week, 50$ per day
Q3:How Many spare parts you will prepare for customer?
A3: Spare parts included: mould clamp, long and short nozzle,heating band,Wrench,Switch,Thermocouple,Operation manual
      Tool box,Lubricate Oil,Sealing,Filter etc.
Q4:Computer sytem,Except English, can you change other language,say: French,Spanish,Arabic,Russian.
A1:Yes,when you place order,please tell us the language which you required. Standard one with English,Japanese,Chinese,Korea.
Q5:Can you change the power source for us? Say:we need 3Â Phase 220V 60HZ
A5: When you place order,please write clearly.Then we will change the electric system for you.
Q6:If i Need Green Color machine,can you do it for us?
Q7: Yes,please give us the color sample.So we can do it for you.
Â
Cindy Zhang
Â
Â
Tel:+86 18368093243
 Â
Http://www.china-haijiang.com
Ningbo Haijiang Machinery Manufacturing Co.,Ltd.
Address:Next to the treasure Bringing the road, Yinzhou District, Ningbo (Tong Industrial Zone)
Â
Â
Metal Stamping Parts
Stamping (also known as pressing) is the process of placing flat sheet metal in either blank or coil form into a stamping press where a tool and die surface forms the metal into a net shape. Stamping includes a variety of sheet-metal forming manufacturing processes, such as punching using a machine press or stamping press, blanking, embossing, bending, flanging, and coining.[1] This could be a single stage operation where every stroke of the press produces the desired form on the sheet metal part, or could occur through a series of stages. The process is usually carried out on sheet metal, but can also be used on other materials, such as polystyrene.Stamping is usually done on cold metal sheet. See Forging for hot metal forming operations.
Main particulars
10
|
MAIN PARTICULARS |
Material |
iron, carbon steel, stainless steel, brass, copper, alloy steel, aluminum, cold rolled steel with various plating |
Standard |
ASTM, ASME, DIN, JIS, ISO, BS, API, EN |
Certificate |
ISO9001, BV |
Dimension |
As per drawing, as large as we can |
Processing |
Laser/Line cutting, Stamping, CNC Punching, CNC Bending, Welding, Assembling, ect. |
Finishing surface |
Machined surface with tectyl891, blasting and painting(Hempel, Inter, Sigma, Jotun), anodize, polishing, zinc plated, nickel plated |
Marking |
as per clients` requirements |
Inspection |
material, construction, dimension, heat treatment, hardness, NDT |
Quality |
ISO9001, BV, PPAP control production |
Lead time |
5 days for sample, consult with customer for mass production |
Delivery |
Express for sample, ocean shipping/air for mass production |
Our Capabilities |
CNC Machining, CNC center machining, drilling, milling, turning, grinding, tapping, forging, stamping |
Engineering&manufacturing services |
R&D process, tooling and gauging design, product design Integrated CAD/CAM system, test and measuring |
Technology |
Professional tooling design as per drawings and samples |
Others |
Recyclable, in line with environmental requirements and standards, and reliable |
Stamping is by press and die for sheet, strip, pipe and profiles, such as outside force, to produce plastic deformation or separation, to obtain the required shape and size of the workpiece forming method (stamping).Stamping and forging belong to plastic processing (or pressure processing), called the forging press.Stamping of billet is mainly hot rolling and cold rolling steel plate and steel belt.Steel all over the world, there are 60 ~ 70% is plank, most of them after punching into finished products.Car body, chassis, fuel tank, radiator fin, boiler drum, the container shell, motor, electric iron core silicon steel sheet stamping processing.Instruments and meters, household appliances, bicycles, office machinery, household utensils, and other products, also have a large number of stamping parts.
Stamping processing is the use of conventional or special equipment of the power, the deformation of sheet metal in the mould is directly force and deformation, thereby gaining a certain shape, size and performance of the production technology of product parts.Sheet metal, stamping mould and equipment is processing of the three elements.According to the stamping processing temperature is divided into hot stamping and cold stamping.The former is suitable for the deformation resistance is high, poor plastic sheet metal processing;The latter at room temperature, it is commonly used plate stamping method.It is metal and plastic machining (or pressure) is one of the main methods, also belongs to the material molding engineering technology.
Used by stamping mold known as the stamping die, die for short.Die is the material (metal or non-metallic) processing into salt pieces of special tools required.Is of vital importance to the die in stamping, did not conform to the requirements of punching die, stamping production batch is difficult;No advanced punching die, stamping process of advanced cannot achieve.Stamping process and die, stamping equipment and materials to form the three elements of stamping processing, can only draw stamping them together
Stamping Parts
Stamping Parts,Precision Metal Stamping,Custom Stamping Parts,Metal Stamping Parts
UniSite Group , http://www.unisitemachining.com